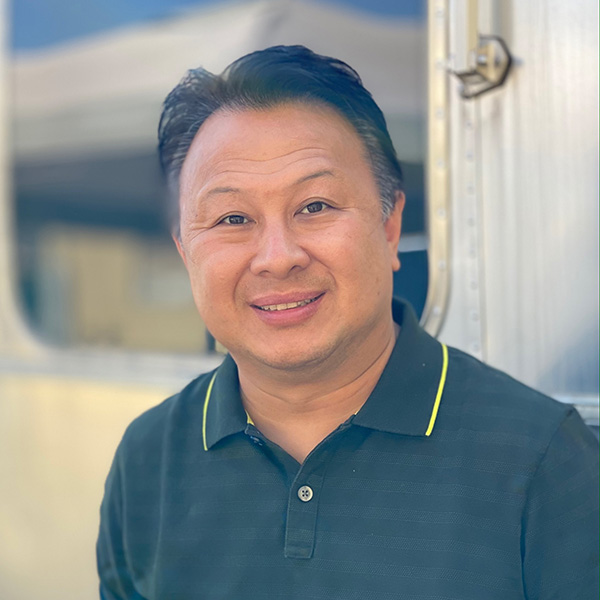
Christian Tse understands the skill it takes to create a handcrafted piece of jewelry. After all, he’s been doing it since he was a youngster; in fact, his father had him sizing rings at the family business, earning a quarter for each completed piece.
But the designer also sees the future of jewelry, and it is through technology. Tse says this stage of his career has him looking at the engineering behind how jewelry is made, and he is more excited than ever to see where it is going.
“After 30-plus years in this business, it feels like it is really just the beginning for me,” Tse says. “Many of the plans and processes I have wanted to implement are starting to happen now. I finally have the resources and abilities to invest in the technology I’ve always dreamed of. The technology nerd in me is loving it.”
Tse’s family came from Cambodia but are of Chinese descent. They have always been in jewelry, he says, creating traditional Chinese designs for weddings and special events. Tse says he, too, was born into the trade—as Tse grew up, he worked alongside his parents and attended the Gemological Institute of America to establish his own expertise.
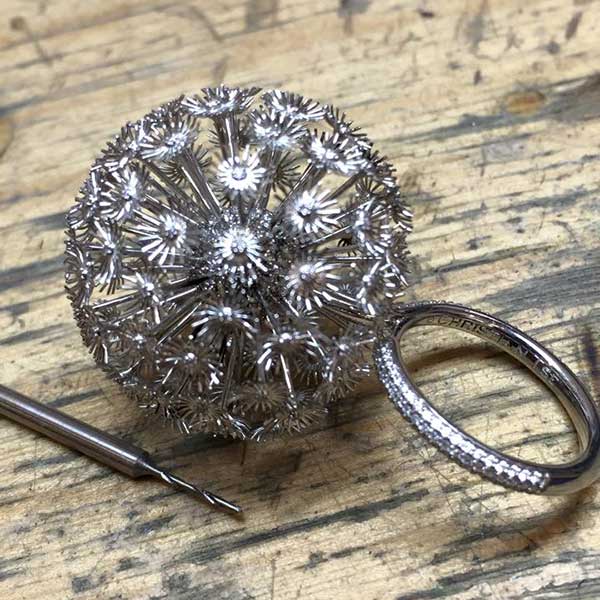
He founded Christian Tse Designs in 1996. From the start, Tse has worked with dozens of editors, stylists, and celebrities who wore his signature statement pieces on the runway. His work always seemed to defy traditional techniques, and his client list grew because of it; picture Michael Jackson in that mesh tie or J.Lo and Beyoncé wearing his designs. Big opportunities also came his way—Tse even created the pink diamond ring used in the Steve Martin remake of The Pink Panther.
Now, his California studio still has its traditional jeweler’s benches. But it also has a wide array of high-tech machines that produce his latest designs. That includes new technology and techniques that Tse says will move design into the fast lane—all while keeping people front and center on the creative side of the business.
“Automation will be a big trend moving forward when it comes to fine jewelry manufacturing—automating processes that would have previously been done by hand but will soon be handled by machines,” Tse says. “Examples include polishing, sorting, and quality control. At my factory, we have developed incredible robotics for polishing. It is exciting because it greatly increases productivity and efficiency, plus it ensures a precision that is near impossible by hand.
“As a bench-trained goldsmith, I am amazed at what these new robots can do when it comes to precious-metal polishing,” Tse says. “Machines for sorting and quality control are also going to streamline manufacturing and help us to create better jewelry much more efficiently.”
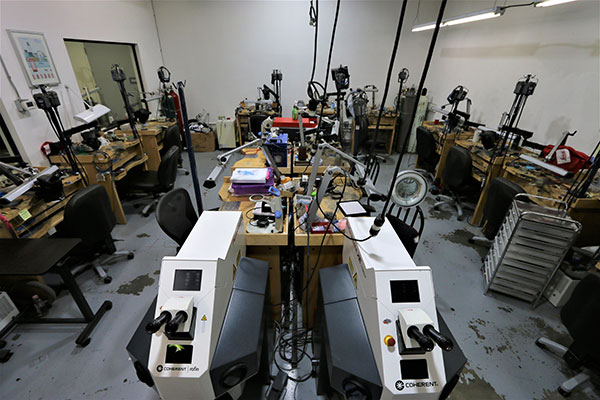
He says he is investing in research and development of direct 3-D precious- metal printing, and he hopes to reveal some new products related to this work in the months to come. Tse says he is most excited about the manufacturing side, specifically processes his company is using to boost its quality, including what he calls high-heat isostatic pressure.
“HIP [high isostatic pressure] is a process of taking casted or printed metal to high heat along with high pressure [of about 30,000 psi],” Tse says. “That combination pushes any sub-service micro porosity out of the metal and makes the pieces 100% dense. It is a true quality enhancement to our manufacturing process, as it makes our jewelry pieces very dense and in turn makes them shinier than without the process. It’s a visually different product of jewelry when pieces go through a HIP cycle.”
Yet without the right people behind these processes, the work cannot be done in the way that his brand demands, he says.
“People are your business’s most important assets,” Tse says. “The more I invest in my team and keep my standards high, when it comes to working only with the best, the more successful our manufacturing business becomes.
“Groundbreaking things are coming soon, and I am confident it will be beneficial for everyone in fine jewelry, streamlining the process from concept to creation so that our customers can always have new, exciting, and relevant jewelry,” Tse says.
Top: Christian Tse has had a 30-year career in jewelry, and his own family has been in the industry for more than a century. Yet he still gets excited about the future of the business and where technology is taking it (photos courtesy of Christian Tse).
Follow me on Instagram and Twitter
Follow JCK on Instagram: @jckmagazineFollow JCK on Twitter: @jckmagazine
Follow JCK on Facebook: @jckmagazine